Virtuelle Durchsatzsimulation: Optimierte Anlagenplanung durch digitale Testszenarien
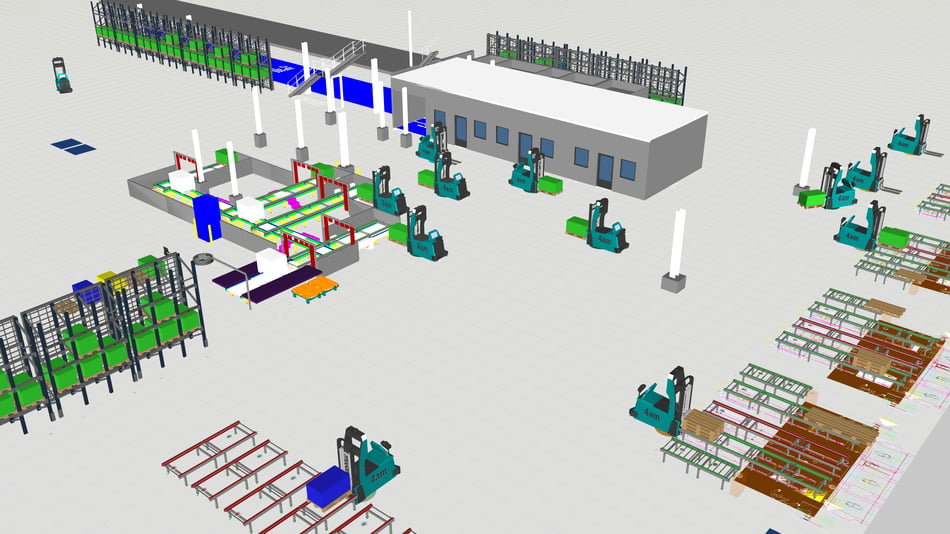
In der modernen Industrie ist es entscheidend, Prozesse so effizient wie möglich zu gestalten. Doch bevor neue Anlagen oder Erweiterungen realisiert werden, stehen Unternehmen vor zahlreichen Fragen und herkömmliche Planungsmethoden stoßen oft an ihre Grenzen: Prozesse laufen nicht wie erwartet, Kapazitäten sind schwer vorhersehbar, und Anpassungen während der Inbetriebnahme kosten Zeit und Geld. Wer sich bei diesen Themen nur auf theoretische Berechnungen verlässt, geht hohe Risiken ein. Genau hier setzt die virtuelle Durchsatzsimulation von SCIO Digital an – eine innovative Methode, um Abläufe zu testen und zu optimieren, bevor sie in die Realität umgesetzt werden.
Vom Konzept zur Simulation: Wie eine Anlage vor ihrer Umsetzung optimiert wird
Unser aktuelles Projekt bei einem renommierten Automobilhersteller zeigt eindrucksvoll, wie Unternehmen mithilfe einer Simulation realitätsnahe Einblicke in ihre Prozesse gewinnen können. In der bestehenden Anlage des Kunden sind bereits 7 autonome Gabelstapler von unserer Schwestergesellschaft 4am Robotics im Einsatz, ergänzt durch einige manuell gesteuerte Stapler. Ziel der Erweiterung war es, auch die verbleibenden manuellen Stapler des Kunden durch zusätzliche autonome Fahrzeuge von 4am zu ersetzen. Die Simulation sollte dabei prüfen, ob die geplante Anzahl an autonomen Staplern ausreicht, um den Materialfluss effizient zu steuern – ohne Engpässe oder unnötige Überkapazitäten.
Die Simulation erstellte dafür eine detaillierte digitale Umgebung, in der alle Prozesse unter realitätsnahen Bedingungen getestet wurden. Das Besondere: Die gesamte Materialfluss-Simulation basierte auf echten Produktionsdaten des Kunden, um möglichst präzise Ergebnisse zu liefern.
Die Ergebnisse zeigten, dass 8 weitere autonome Stapler (AFi-M) von 4am Robotics notwendig sind, um die erforderlichen Transportaufgaben zuverlässig zu übernehmen. An einem Arbeitstag von 17 Stunden werden ca 2390 Palettentransporte durchgeführt, darunter 1989 Vollgut-Paletten, 277 Leergut-Paletten, 96 leere Deckelgestelle sowie 23 unklare Produktpaletten, die gesondert geprüft werden müssen.
Simulation unter realen Bedingungen: Einblicke in den Prozessablauf
Die Simulation beginnt mit der Anlieferung der Vollgut-Paletten an vier Quellen. Die Paletten werden gescannt und von den AMRs aufgenommen, bevor sie zu den fünf vorgesehenen Senken (Zielorte) an den Förderbandstationen transportiert werden, die das Material in die nächsten Produktionsschritte leiten.
Ein zentraler Aspekt der Simulation ist die Berücksichtigung von realen Produktionsschwankungen. In der Realität laufen Produktionsschritte nicht immer exakt im Sekundentakt ab. Um diese Schwankungen auszugleichen, sind 180 Pufferplätze in 20 Regalen mit je 9 Stellplätzen vorgesehen. Paletten, die nicht sofort weiterverarbeitet werden können, werden dort zwischengelagert. Ein weiterer Mechanismus zur Prozessoptimierung ist die variable Abgabezeit der AMRs an den Stationen. Nicht jeder Stapler benötigt die gleiche Zeit für die Übergabe einer Palette – einige Fahrzeuge brauchen nur 8 Sekunden, während andere bis zu 30 Sekunden einplanen. Diese variierenden Übergabezeiten der AMRs werden gezielt simuliert, um Rückstaus zu erzeugen und einen möglichst realitätsnahen Ablauf abzubilden.
Parallel dazu werden Leergut-Paletten aus zehn Quellen entnommen und an acht Senken abgegeben, während Deckelgestelle aus sechs Quellen zu den entsprechenden Lagerplätzen transportiert werden. Die unklaren Produktpaletten werden an sieben separate Senken geliefert, um eine gesonderte Prüfung zu ermöglichen.
Fehlersimulation und Reaktionsfähigkeit
Ein weiterer Vorteil der virtuellen Durchsatzsimulation ist die Möglichkeit, ungeplante Störungen realitätsnah zu simulieren. In der Simulation können zufällige Fehlerfälle auftreten – beispielsweise kann ein AMR an einer beliebigen Stelle ausfallen. Die übrigen Fahrzeuge müssen daraufhin ihre Routen und Aufgaben anpassen, um den Materialfluss aufrechtzuerhalten. So kann simuliert werden, ob die Flotte in der Lage ist, solche Störungen effizient zu kompensieren, ohne dass es zu erheblichen Verzögerungen kommt.
Insgesamt wurden in der Simulation 3780 Transportaufträge erfolgreich abgeschlossen, mit einer gesamten Fahrstrecke von ca. 276 km für die gesamte Flotte. Diese Daten ermöglichen es, potenzielle Schwachstellen zu erkennen und bereits im Vorfeld zu optimieren.
Virtuelle Begehung durch VR-Integration
Neben der Prozessoptimierung ermöglicht die Durchsatzsimulation auch eine frühzeitige Schulung der Mitarbeiter. Mithilfe einer VR-Brille können Anwender die Anlage bereits vor der Realisierung virtuell begehen. Dadurch erhalten sie einen detaillierten Überblick über die Abläufe und können sich bereits vor der Inbetriebnahme mit der Umgebung vertraut machen. Somit ist das Personal bereits eingearbeitet, bevor die Anlage in den Live-Betrieb geht.
Die Zukunft der Durchsatzsimulation: Mehr Effizienz durch digitale Testszenarien
Dieses Projekt zeigt eindrucksvoll, wie Unternehmen mit einer virtuellen Durchsatzsimulation Fehlentscheidungen vermeiden, Ressourcen optimal nutzen und den Produktionsstart effizient vorbereiten können. Statt erst in der Realität auf Probleme zu stoßen, können Unternehmen ihre Prozesse bereits im Vorfeld validieren, optimieren und kostspielige Fehler vermeiden.
SCIO Digital bietet diese Durchsatzsimulation für Unternehmen verschiedener Branchen an – von der Automobilindustrie über die Fertigung bis zur Logistik. Mit modernen Simulationsmodellen können Materialflüsse, Kapazitäten und Prozessabläufe realistisch getestet und optimiert werden.
Mehr Infos über unsere innovativen Services finden Sie hier.