Raise the Curtain for the Potential of Virtual Commissioning
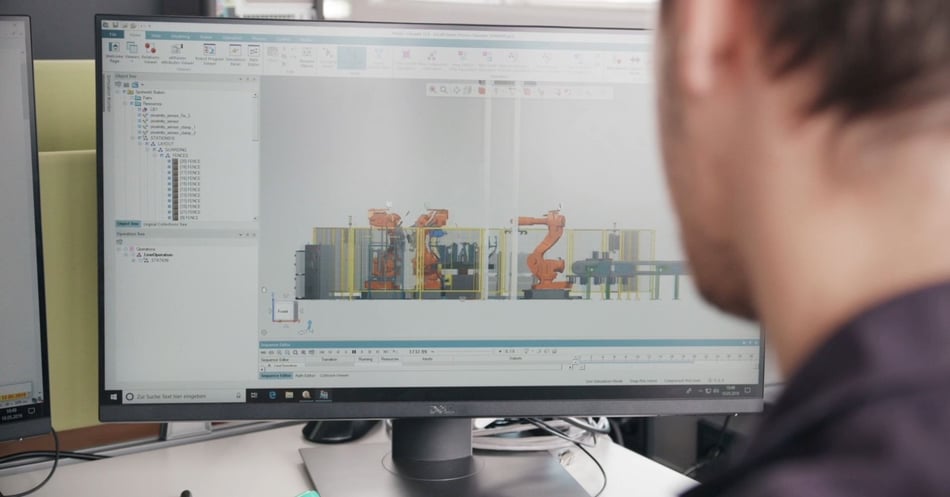
What do a ballet performance and virtual commissioning have in common? At first glance, not much, but they are enormously similar in their approach: planning, rehearsing, correcting - until every detail of the choreography and every movement of the dancers are rehearsed. In the case of virtual commissioning, the control software of the installation is played in, tested and optimized on a virtual model in an early phase of the realization. This is often done in conjunction with a cinematic 3D representation of the system. Errors can thus be detected and corrected before the actual commissioning, so that the "premiere" runs smoothly. In our plant projects, such as the conversion of a final vehicle assembly line with an electric monorail system (EMS), virtual commissioning has therefore been an obligatory component for several years. However, there are often still reservations among many mainly medium-sized mechanical and plant engineers:
"The setup of the virtual model is often seen as purely an additional expense. We usually hear statements like: 'Our plants are too complex or the plant changes too often to model it.' However, this is exactly where virtual commissioning plays out its great potential" - explains Ulrich Reiser, CDO SCIO Automation.
What exactly are the advantages of Virtual Commissioning for our customers?
-
Validation of the plant control system before commissioning
Without virtual commissioning, testing of the control system is only possible on the real plant. But an ensemble would never go on stage without a dress rehearsal, right? Especially essential for complex choreographies. With the virtual commissioning as a virtual dress rehearsal, we check especially complex systems for possible logic errors, which in the worst case can mean downtimes for the end customer. After all, no "dancer" should deviate from the choreography at the grand entrance! In this way, we not only ensure product and process quality, but also significantly minimize the effort and thus costs for potential subsequent adjustments in the program. Downtimes are a major problem, especially in series production in the automotive industry. For orders like our EMS project, it was therefore crucial to use virtual commissioning to identify potential problems and logic errors in the plant PLC beforehand and to specifically prevent them by making adjustments. Within the first two days after commissioning, the plant was already running so stably that we were able to exceed all production targets.
-
Increased flexibility in the course of the project
By using virtual commissioning, we can test the plant and its control system in a systematic and efficient way - quite flexibly. For example, if changes to the plant or its environment occur during the project, we can quickly adapt the virtual model at any time and test the changes without risk. In this way, we can not only prevent subsequent and costly adjustments on site, but also ensure that the plant performs perfectly when it makes its grand entrance at the end customer - the commissioning.
-
Shortened commissioning and project lead time
Last but not least, virtual commissioning also facilitates the integration of the machine or system into the real production environment. Although it is not possible to completely dispense with the on-site programmer, the effort required is considerably less. This is an enormous advantage, especially in a globally active industry such as mechanical and plant engineering. As the EMS project shows: Virtual commissioning allows us to successfully overcome challenges, be they scheduling demands or unforeseen obstacles such as the Corona pandemic, and ensure that the project is completed in a short period of time. Instead of being purely sequential, hardware and electrical design, procurement, PLC development and commissioning can also run in parallel. This makes resource planning more flexible, which reduces implementation and project costs. Small and medium-sized companies in particular benefit from these advantages.
"We are continuously working on increasing the efficiency for setting up the virtual model in order to establish virtual commissioning in all projects in the future, regardless of complexity and customer requirements. For example, by extending interfaces for data transfer from previous engineering steps. Our goal is to use the virtual model throughout the entire life cycle of a plant. This enables us to optimally support our customers with regard to remote service and changes during operation. Based on our virtual commissioning process, we have already successfully developed these so-called digital twins in our customer projects," says Ulrich Reiser, CDO SCIO Automation.
Read more about virtual commissioning here.