Global project duo: efficient warehouse management for car body production
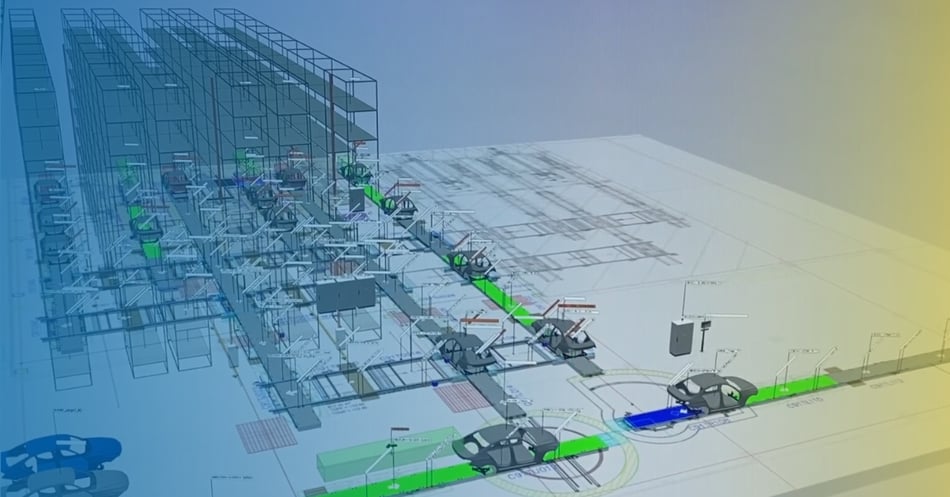
Let's head to China and Hungary! Our international team is developing and implementing an entire electrical engineering system for a prominent customer in the automotive industry, along with software for the high-bay warehouses at two production sites. The challenges? Two locations, multiple continents, and a huge range of different requirements to meet.
One project, two worlds:
- Electrical planning
- Control cabinet construction
- Installation
- (Virtual) commissioning
Car bodies are set to be transported between painting and assembly stations, and a high-bay warehouse using a floor conveyor system on the production sites of an automotive manufacturer in China and Hungary. Our own warehouse management software is taking care of managing the storage spaces in the rack (aisle, box number) and retrieving the body shells. The production sequence for painting and the retrieval sequence leading to final assembly are dictated by the customer's overarching control system. The differences between the projects in Hungary and China are numerous, despite the fact that the tasks are fundamentally the same. While the existing high-bay warehouse is being expanded in China, our team in Hungary is part of an exciting greenfield project: building an entirely new production site.
Greenfield vs. Brownfield:
The original project began three years ago with the construction of the high bay warehouse in China, including virtual commissioning. Successful collaboration with VESCON on virtual commissioning led to the warehouse being put into operation without a hitch. The expansion was also carried out without any issues thanks to the efforts and dedication of our on-site team in Shenyang, China, along with another virtual commissioning deployment. We were able to keep costs and personnel numbers to a minimum as a result. The contract was awarded in late 2022, and the warehouse system in China has been operational since September, with final acceptance scheduled for April of this year.
Implementing a warehouse control system in Hungary by involving virtual commissioning to enable us to build a new production site is significantly more complex. Lots of logistical challenges need to be overcome in the initial phase of plant construction, and warehouse management efficiency plays a crucial role here. Our flexible Warehouse Management System ensures that the inbound and outbound processes for vehicle bodies are handled effectively in a flexible way. It can also be seamlessly integrated into the end customer's higher-level control system. Thanks to our extensive experience and virtual commissioning, the electrical engineering processes and software integration proceed as planned.
![]() |
By collaborating with a real-time simulation software provider, the virtual commissioning process has also become the largest successful simulation ever conducted at the end customer's premises.
|
Due to the positive progress of the project, the assembly and warehouse area in Hungary is scheduled for completion by the end of 2024.
Interested in our warehouse solutions? Learn more about what we can offer for your intralogistics here.
Meet our warehouse experts at LogiMAT 2024. Find out everything you need to know about our exhibition appearance here.