VitaCube high-bay warehouse: setting the standard for green intralogistics

With a daily output of over 1.2 million products, Vitakraft — one of the leading pet food manufacturers — faced a classic challenge: full order books but not enough warehouse space. Initially, decentralizing storage seemed like a quick fix, but it caused inefficient on-site traffic and rising emissions. The solution? Vitakraft’s new high-bay warehouse, VitaCube, at their Achim/Bremer Kreuz site, offers a sustainable answer to logistical, economic, and environmental demands. And at the heart of it all: our subsidiary MFI, the general contractor for the project and a longtime expert in automated intralogistics for the food sector.
Project highlights at a glance
![]() |
|
Challenge
From growth to bottleneck
With more than 1.2 million items produced every day, Vitakraft faced growing demands — more products, but less space. At the same time, the pressure to deliver fast and reliably was rising. While decentralized warehouses offered a temporary solution, they also caused increased site traffic, complicated processes, and higher emissions. Recent events like the pandemic and geopolitical crises showed how vulnerable and hard to manage decentralized setups can be. What Vitakraft needed was a centralized, scalable, and automated solution.
Our solution
The VitaCube — a fully automated high-bay warehouse, delivered turnkey
At their main Achim site, we built a fully automated high-bay warehouse that centralizes all intralogistics processes, connects them digitally, and rethinks them with sustainability in mind. We kept the plant running throughout construction and seamlessly integrated the new facility into the existing infrastructure.
On just 4,000 square meters, the warehouse holds 44,000 pallet spots. This was made possible by combining smart conveyor technology, fully automated controls, and optimized space utilization. From goods receipt to outbound shipping, every step is digitally managed and efficiently linked. Each pallet is automatically tagged with RFID, double-stacked, wrapped in stretch film, and transferred via vertical conveyor to the electric floor conveyor system. From there, 25 shuttles take over — moving at 2 meters per second across five aisles, handling up to 230 pallet movements per hour.
Our in-house developed software EDY manages warehouse operations, material flow, and connects directly with Vitakraft’s SAP system, ensuring full transparency and control — even as complexity grows.
"Digitalization ran like a red thread through every phase — from planning to commissioning."
— Abraham Aslanidis, Sales Director MFI
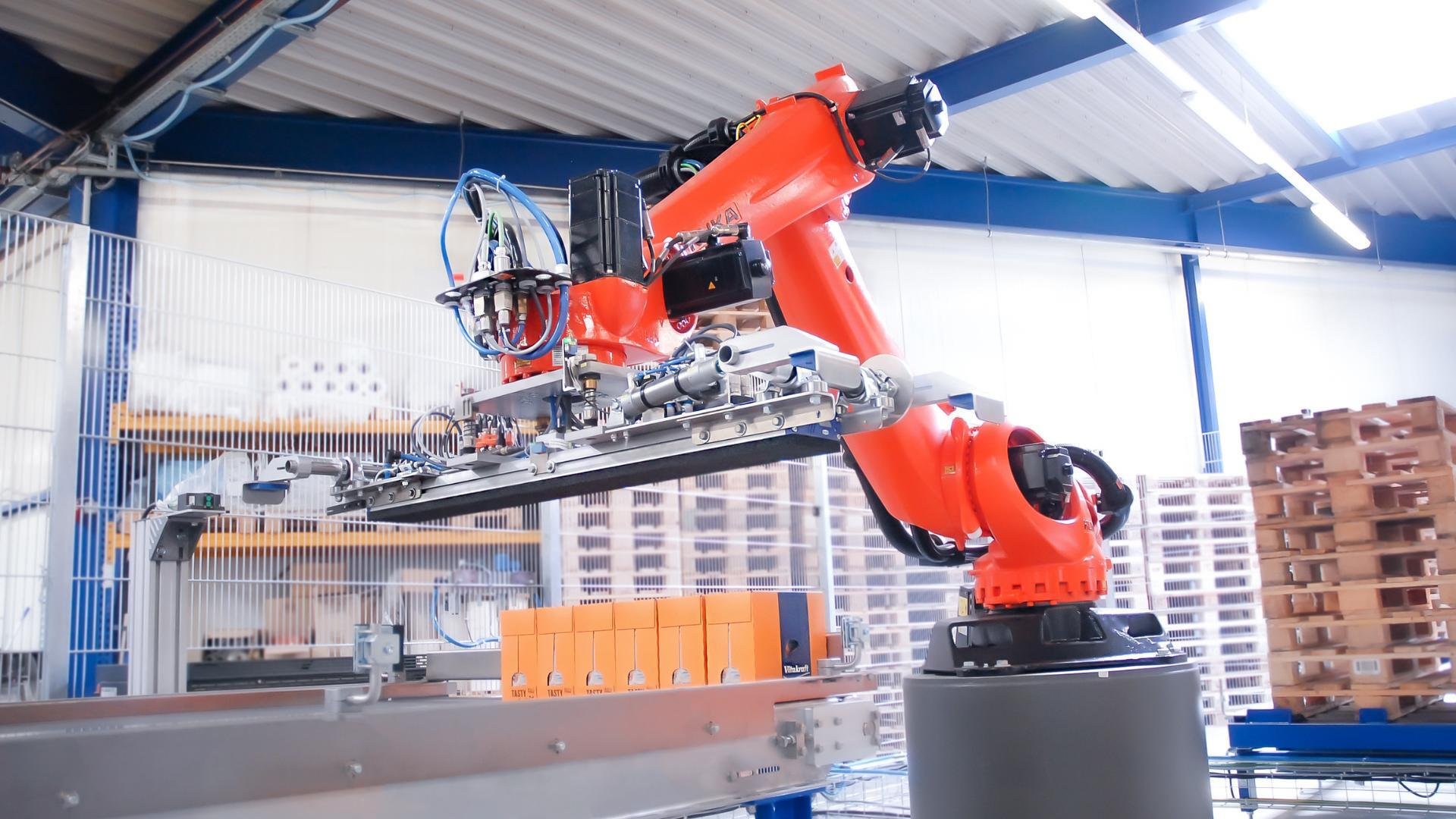
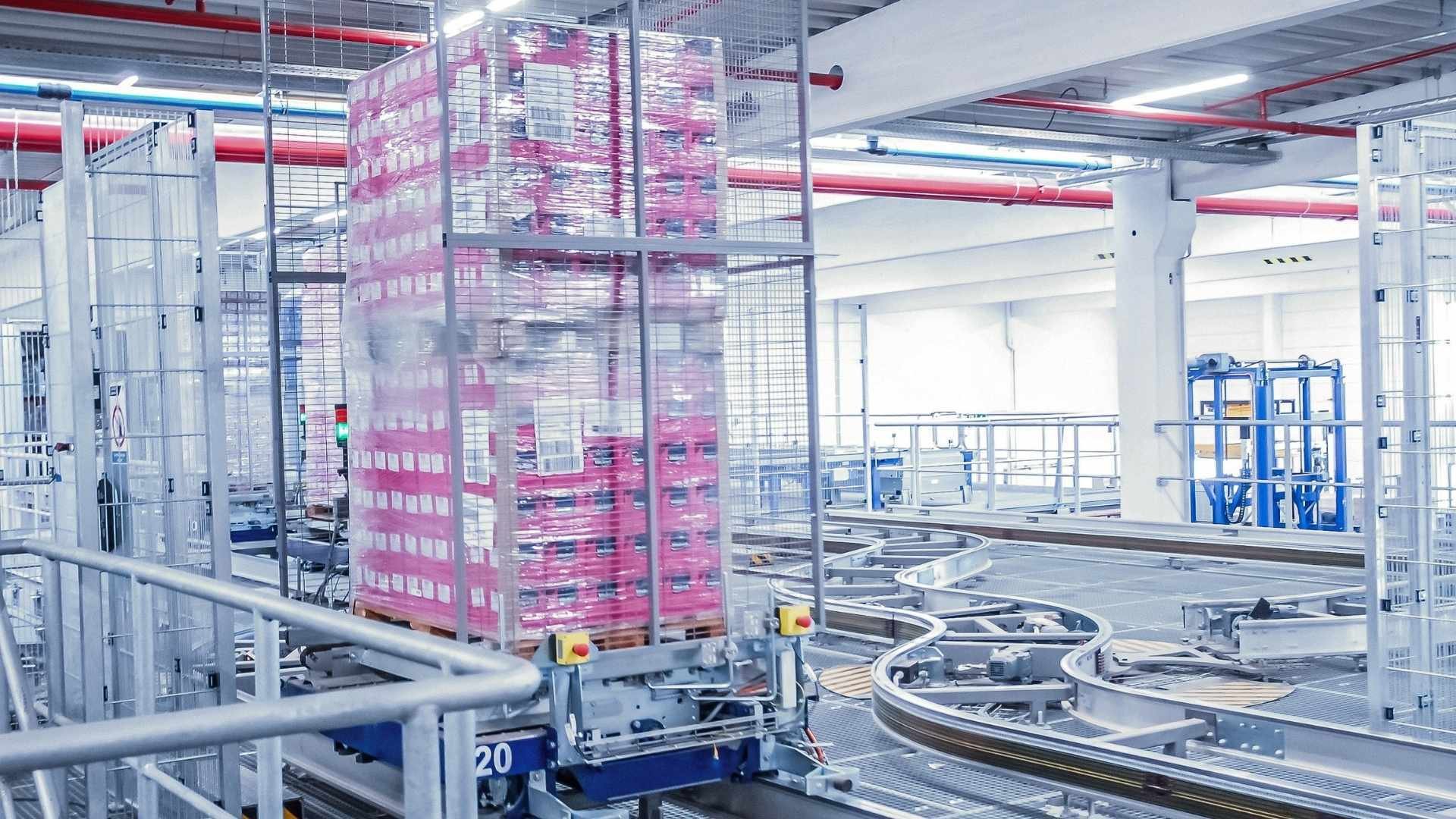
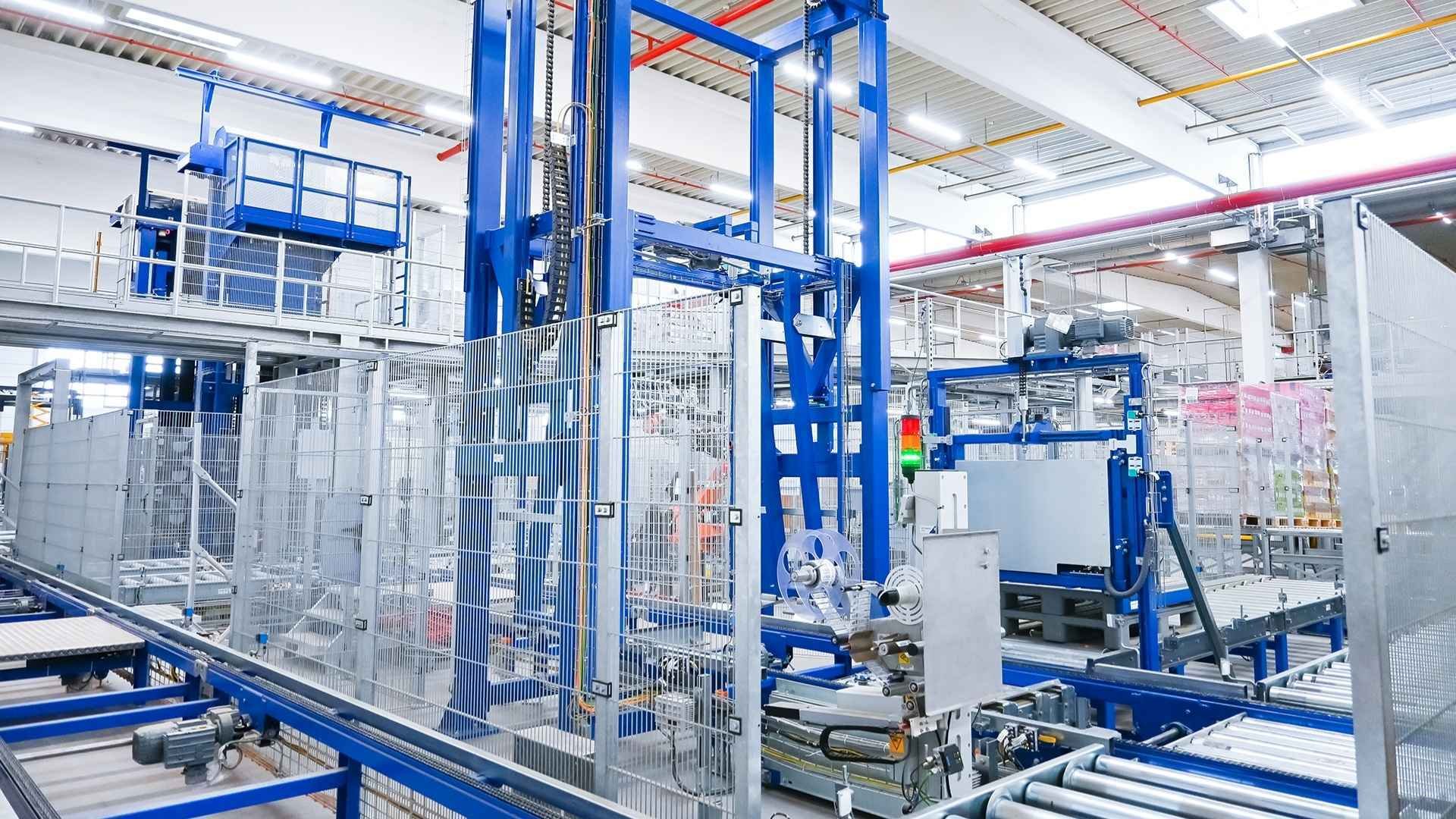
A standout feature:
A 40-meter-long suspended bridge connecting the new VitaCube to existing buildings — both structurally and functionally. We integrated numerous existing structures and rail systems, significantly boosting site flexibility.
By the way:The VitaCube stands 37 meters tall — as tall as the Plaza of Hamburg’s Elbphilharmonie. But in the sensitive food industry, size isn’t everything. Thoughtful, hygienic design matters just as much. Learn more about our hygienic intralogistics solutions here.
Sustainability is at the core:
Centralizing all warehouse operations eliminated external storage and reduced on-site traffic — saving Vitakraft about 12,000 liters of diesel every year. At the same time, automation lowers the need for manual labor — a huge advantage in today’s tight labor market. Many companies struggle to implement sustainable logistics due to lacking infrastructure and technology. With VitaCube, we’re proving a different way — the beating heart of Vitakraft’s international distribution network and a tangible example of efficient, sustainable intralogistics.
"VitaCube proves that efficient intralogistics and climate protection are not mutually exclusive."
— Abraham Aslanidis, Sales Director MFI
Want to learn more about our vision for sustainable industry and our detailed solutions?
Facing similar challenges? We’re here to support you — from initial idea through turnkey implementation.