The way for successful local & automated cable assembly
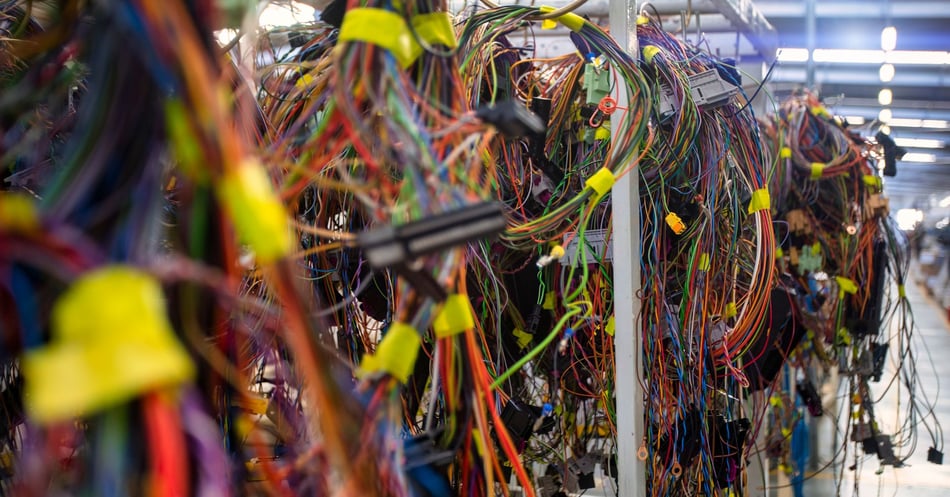
Cable harnesses are still assembled manually because they’re so unique and complex? Production is relocated to low-wage countries as well to keep costs low? Numerous manufacturers are familiar with these problems. This is a risky strategy for manufacturing companies given the accelerating rate of climate change worldwide and uncertain political events. The solution: innovative automation technologies from the smart factory!
In order to protect a well-known supplier to the automotive industry from these problems, our experts at VESCON Systemtechnik are relying on innovative and customized automation solutions in a joint project, that allows their customer to benefit in a variety of ways. How do our experts make this possible?
1. They declaring war on non-rigid components
Non-rigid components such as cable harnesses can stop automation solutions becoming a reality for your cable assembly due to unwanted deformations. This is where customized workpiece carriers are massively needed! These helpful tools enable:
• The cables to be guided into the best position
• The cables to remain in the desired position during the entire assembly process
• The cable harnesses to be connected at specially defined fixed points
How can workpiece carriers be designed in the best way possible?
Our Team relies on 3D printing to produce ideal workpiece carriers for our customer. Using 3D printed molded parts, our experts first create models for the workpiece carriers. Using these models, they can then the cable’s position and alignment, as well as their connections. If the cable routing is not yet as effective as it can be, the 3D models are improved upon. This is done in a kind of feedback loop:
First, a digital 3D model is constructed, the position of the cable in it is simulated and then 3D printed. By repeating this process, an ideal model is produced at the end. The finished workpiece carrier is manufactured based on this.
![]() |
![]() |
What are the benefits of 3D printing?
• Saving an enormous amount of time and money:
Cheaper and quick to produce 3D models, instead of costly/time-consuming conventional manufacturing in the optimization phase.
• Conserving resources:
By eliminating the need for numerous prototypes
• Making the best use of the available space:
This is made possible by ensuring the cables remain in the ideal position
• Optimizing accessibility for automatic processes:
Critical points for automatic testing and assembly are clearly visible and easily accessible due to the cables being in the ideal position
2. Our experts always keeping product quality in mind
Guaranteeing that the wiring harnesses remain in the ideal position and are properly fixed is essential for ensuring that a wiring harness can be installed and connected without any issues in the confined installation space of the car. Incorrect processing can create in sharp edges and, in the worst case, result in dangerous short circuits.
How can we ensure that the cable harnesses are assembled with a perfect fit?
The automated camera inspection makes it possible.
Most camera systems are designed to detect deviations down to the smallest millimeter. However, they can tolerate minimal deviations due to the fact that the components are flexible. The focus in this case is on inspecting the position, the rotations as well as the crossings of the cable harnesses. This is easy to recognize for the human eye, but for but it’s a huge challenge for automated systems, our automation specialists apply an innovative method, giving our cameras the tools to make intelligent decisions in the same way as humans do:
Machine learning
By teaching different product images into the specially developed camera system, knowledge is generated on how to assess the cable routing. Based on negative and positive examples, the system searches for a comparison to the object being tested, making a decision on its quality. These form a kind of progression in terms of their tolerance to the best position, to enable a step-by-step approach to be taken. In other words, there are images that show a very poor cable position, images that are already slightly better, and then sample images that show the best possible position.
3. Many years of experience and expertise
VESCON Systemtechnik is on hand to help as an experienced partner in this project with comprehensive expertise in developing process- and cost-optimized special machines. As a manufacturer and automation service provider, we rely on a winning combination of integration, innovation and mechanical engineering expertise, and offer a vast suite of services from developing your solution concept, to production.
The result? An automated cable assembly plant that is ready for the challenges of the future.
Learn more about our innovative solutions here.